Rubber End Cap
Rubber End Cap Manufacturer in the Philippines | RK Rubber Enterprise Co.
RK Rubber Enterprise Co. is a trusted rubber end cap manufacturer in the Philippines, offering high-quality products catering to various industries, including automotive, industrial, and engineering. With a strong reputation for quality and customer service, the company specializes in designing and manufacturing rubber end caps that provide effective sealing, protection, and customization options. Their products are made from high-grade EPDM and silicone materials, ensuring durability and resistance to abrasion and chemicals. By understanding the importance of precision and quality control, RK Rubber Enterprise Co. delivers reliable and efficient solutions for diverse application needs, exploring which can reveal tailored solutions for specific projects.
Key Points
- RK Rubber Enterprise Co. is a trusted manufacturer of high-quality rubber end caps in the Philippines.
- They offer various types, including shrink-fit, adhesive-backed, and slip-on rubber end caps for different applications.
- Their rubber end caps are made from durable materials like EPDM and silicone, ensuring chemical and abrasion resistance.
- RK Rubber Enterprise Co. prioritizes quality control through visual checks, dimensional assessments, and performance testing.
- They cater to diverse industry needs, providing tailored solutions for automotive, industrial, and engineering sectors.
Why Choose Rubber End Caps
The selection of rubber end caps as a protective solution is a wise choice for industries seeking to safeguard equipment, enhance safety, and assure efficiency. By utilizing rubber end caps, companies can prevent damage to tubes, pipes, and other objects, thereby reducing the risk of leaks and contamination. This protective measure is particularly vital in high-stakes environments such as automotive, industrial, and engineering sectors where the integrity of equipment is paramount.
Rubber end caps also contribute to a safer working environment by covering sharp edges and preventing injuries. Their use can also improve the aesthetic appeal of products and machinery, lending a clean and finished look. Additionally, the adaptability of rubber end caps makes them suitable for a wide range of applications across various industries. By investing in high-quality rubber end caps, businesses can guarantee the reliability and efficiency of their equipment, thereby minimizing downtime and maintenance costs. This effective protective solution can ultimately lead to significant cost savings and enhanced operational performance.
Types and Features Overview
Rubber end caps are available in a variety of types and feature diverse characteristics, catering to the unique requirements of various industries. These types and features enable the end caps to provide reliable protection and sealing solutions in different operational settings.
Type | Description |
---|---|
Shrink-fit | Provides a snug fit on cylindrical objects, suitable for applications requiring a secure seal. |
Adhesive-backed | Offers a strong bond to surfaces, ideal for applications requiring a permanent seal. |
Slip-on | Easy to install and remove, making it suitable for applications requiring frequent maintenance. |
Rubber end caps are made from materials such as EPDM and silicone, which are known for their chemical resistance, abrasion resistance, and high-temperature performance. These materials enable the end caps to withstand harsh chemicals and physical wear and tear, ensuring their durability and effectiveness. Custom sizes and options are also available for diverse applications, ensuring effective sealing to prevent leaks and contamination.
Manufacturing and Quality Process
Effective production of rubber end caps involves a precise combination of materials, machinery, and processes. At RK Rubber Enterprise Co., we adhere to a stringent manufacturing process to guarantee the highest quality of our rubber end caps. Here’s an overview of our manufacturing and quality control process:
Key Stages in Manufacturing and Quality Control
- Material Selection and Compounding: We carefully select high-grade rubber materials and compounds them according to specific formulations to meet the required standards.
- Tooling and Molding: Our team designs and fabricates precision molds to produce rubber end caps with exacting dimensions and tolerances.
- Quality Inspection and Testing: We conduct rigorous quality control checks at various stages of production, including visual inspections, dimensional checks, and performance testing to guarantee our rubber end caps meet industry standards.
Our commitment to quality and precision is reflected in every aspect of our manufacturing process. By adhering to strict quality control measures, we guarantee that our rubber end caps provide reliable performance and meet the exacting demands of our clients.
Advantages of Using End Caps
Several key benefits are associated with the use of end caps in various industries. One of the primary advantages is their cost-effectiveness, as they provide long-term savings through durability and reliability, reducing maintenance costs due to lower failure rates. End caps are also easy to install, which minimizes downtime and labor costs. Additionally, they offer excellent protective capabilities, shielding the ends of tubes, pipes, and other objects from damage and leaks.
The durability of end caps is another significant benefit, as they can withstand harsh chemicals and are resistant to tearing and abrasion. This enhanced durability leads to reduced replacement rates, resulting in cost savings and increased efficiency. Moreover, end caps can be customized to meet specific requirements, ensuring effective sealing to prevent leaks and contamination. Overall, the advantages of using end caps make them an essential component in various industries, providing a reliable and cost-effective solution for protecting and sealing tubes, pipes, and other objects. By leveraging these benefits, businesses can improve their operational efficiency and reduce costs.
Common Industry Applications
Industry-specific applications of end caps are diverse, ranging from the protection of hydraulic cylinders in heavy machinery to the sealing of electrical components in automotive systems. Rubber end caps are designed to provide effective protection and sealing solutions in various industrial settings.
Some common industry applications include:
- Automotive Systems: Rubber end caps are used to seal electrical components, protect hydraulic cylinders, and cover sharp edges in automotive systems.
- Industrial Machinery: They are used to protect pipes, rods, and tubes from damage during transportation, storage, or handling, and to provide insulation for electrical components.
- Engineering Projects: Rubber end caps are used to provide a sealing solution to prevent the ingress of dust, moisture, and other contaminants that could damage the internal components of machinery or pipes.
Rubber end caps are widely used in various industries due to their versatility, durability, and cost-effectiveness. They provide a reliable and efficient solution for protecting and sealing components, making them an essential component in many industrial applications.
Importance in Mechanical Sector
Within the domain of mechanical systems, rubber end caps play a pivotal role in ensuring the overall performance, reliability, and safety of equipment. These caps protect components from environmental factors and physical damage, enhancing the machinery’s lifespan. By covering sharp or exposed edges, rubber end caps also contribute to workplace safety, reducing the risk of accidents and injuries.
In mechanical applications, rubber end caps are critical in preventing corrosion, rust, and wear and tear on components. They provide an effective sealing solution, preventing the ingress of dust, moisture, and other contaminants that could damage internal components. Moreover, rubber end caps offer insulation for electrical components, helping to prevent short circuits and other electrical issues.
The importance of rubber end caps in the mechanical sector is underscored by their ability to provide a clean and finished look to products and machinery, improving their aesthetic appeal. Additionally, their versatility in various shapes and sizes makes them suitable for a wide range of applications across different industries. Overall, rubber end caps are an indispensable component in ensuring the reliability, efficiency, and safety of mechanical systems. Their benefits extend beyond protection, contributing to cost-effectiveness and extended lifespan of machinery.
Benefits of Customization Options
Customization options for rubber end caps play a crucial role in enhancing their performance, reliability, and overall value to users. By tailoring the design, material, and size to meet specific requirements, users can optimize the functionality and efficiency of their applications. Customization also enables the creation of unique solutions that cater to particular industries or environments, further enhancing the overall performance of the end caps.
Some key benefits of customization options for rubber end caps include:
- Improved fit and seal: Customized end caps can be designed to fit specific pipes, tubes, or rods, ensuring a secure and reliable seal that prevents leaks and contamination.
- Enhanced durability: By selecting materials and designs that match the operating conditions, customized end caps can withstand harsh chemicals, extreme temperatures, and other environmental factors that may affect their performance.
- Increased versatility: Customization options enable the creation of end caps that can be used in a wide range of applications, from industrial and automotive to medical and consumer products.
Choosing the Right Manufacturer | RK Rubber Enterprise Co.
When selecting a reliable manufacturer for rubber end caps, several key factors come into play, as the right partner can greatly impact the end product’s performance, quality, and overall cost-effectiveness. A reputable manufacturer should possess a deep understanding of the rubber industry, with expertise in producing high-quality end caps that meet specific application requirements.
In evaluating potential manufacturers, consider their production capabilities, material sourcing, and quality control measures. A reliable manufacturer should maintain stringent quality control processes to guarantee product consistency and reliability. Customization options and flexibility in meeting specific requirements are also essential.
RK Rubber Enterprise Co. stands out as a trusted rubber end cap manufacturer in the Philippines, with a proven track record of delivering high-quality products that meet industry standards. Our commitment to quality, customer service, and innovation makes us an ideal partner for businesses seeking reliable rubber end caps. We cater to diverse industries, including automotive, industrial, and engineering sectors, providing tailored solutions to meet specific needs.
Frequently Asked Questions
What Is the Typical Lead Time for Custom Orders?
Typical lead times for custom rubber end cap orders vary between 2-8 weeks, depending on complexity, material selection, and production volume, with expedited options available to accommodate urgent customer requirements and project timelines.
Are Rubber End Caps Suitable for High-Pressure Applications?
Depending on material and design, rubber end caps can be suitable for high-pressure applications. EPDM and silicone materials offer excellent chemical resistance and durability, making them viable for high-pressure uses in industries like automotive and industrial.
Do You Offer Any Certifications or Compliance Standards?
We provide certifications and compliance standards, including ISO 9001:2015, ensuring adherence to international quality management systems and meeting industry-specific regulations, such as those in the automotive and industrial sectors.
Can Rubber End Caps Withstand Extreme Temperature Fluctuations?
Depending on the material used, rubber end caps can withstand extreme temperature fluctuations. EPDM and silicone materials are commonly employed for their high-temperature performance, chemical resistance, and ability to maintain sealing properties in varying temperatures.
How Do You Ensure Consistent Product Quality and Reliability?
Consistent product quality and reliability are maintained through rigorous quality control measures, including material testing, dimensional inspections, and performance evaluations, adhering to industry standards and best practices to guarantee high-performance products.
Conclusion
Rubber end caps offer a multifaceted solution for various industries, providing protection, sealing, and insulation. With a focus on quality and innovation, manufacturers like RK Rubber Enterprise Co. cater to specific needs and requirements. Using rubber end caps enhances efficiency, reliability, and safety in applications. Customization options and adherence to industry standards further solidify the importance of these components in mechanical sectors and beyond, driving business success through cost-effective solutions.
Product Gallery
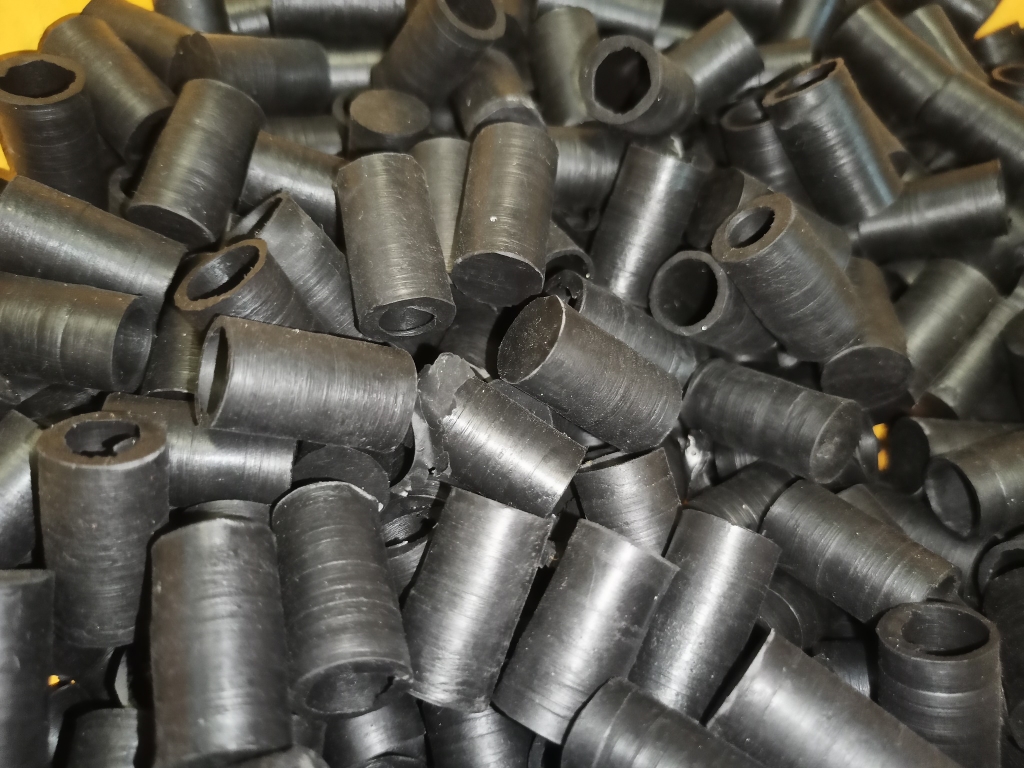
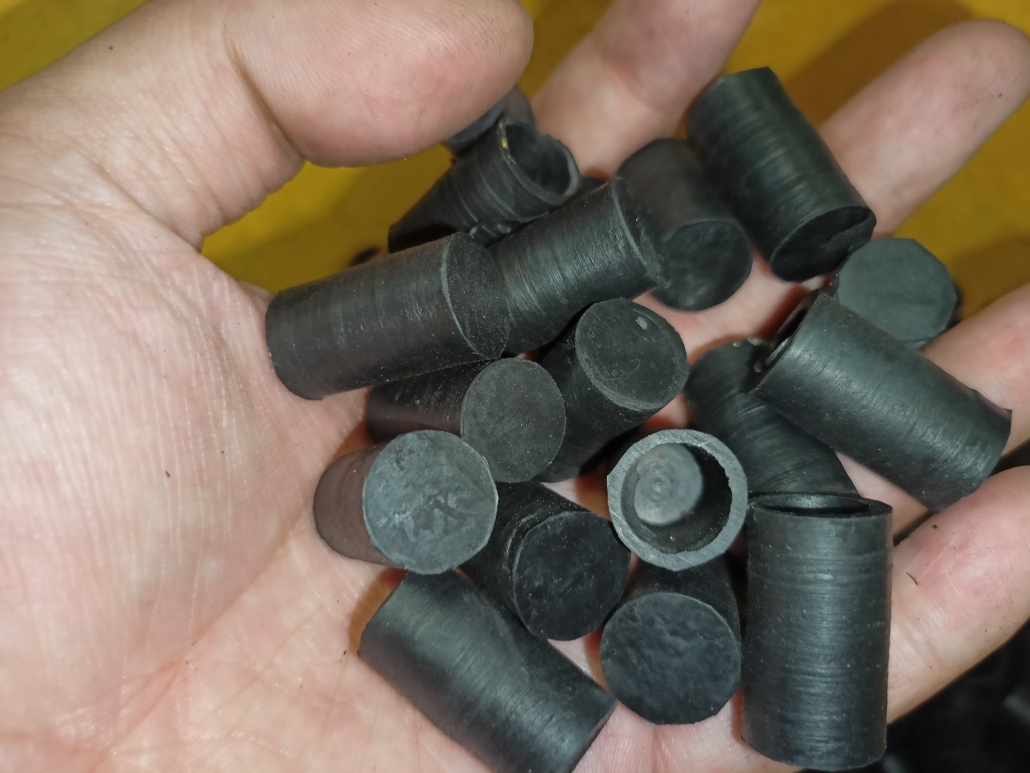
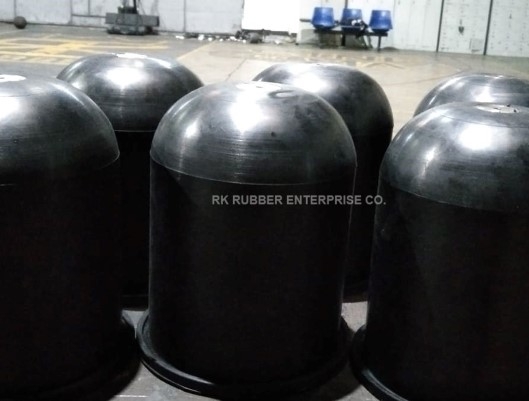
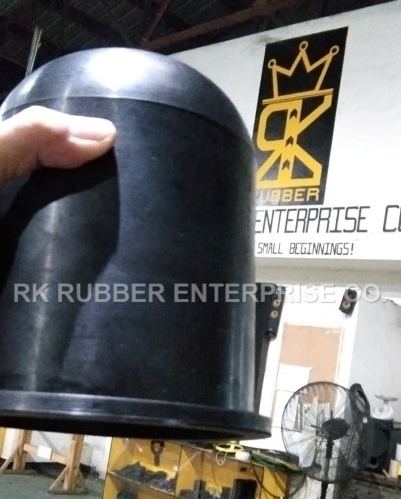
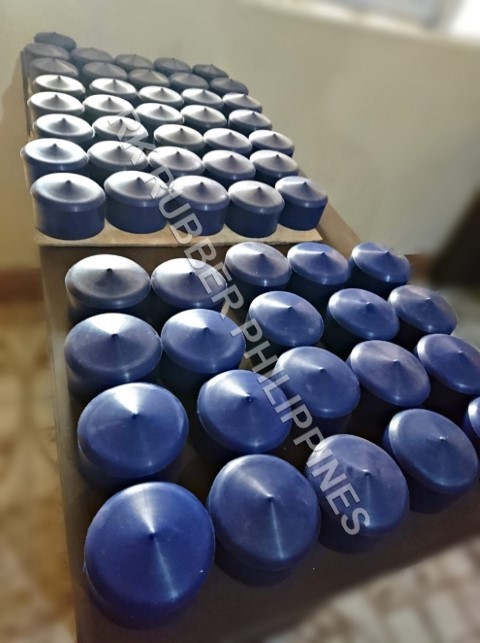
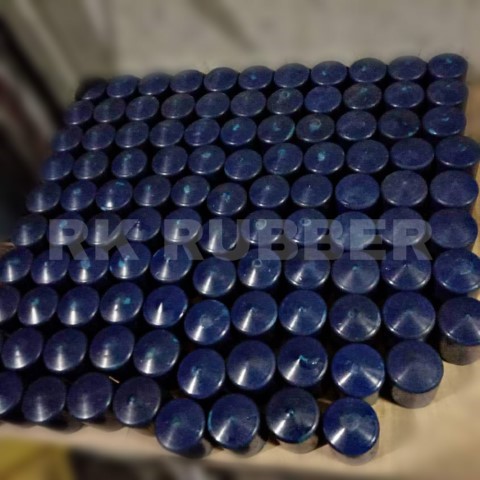
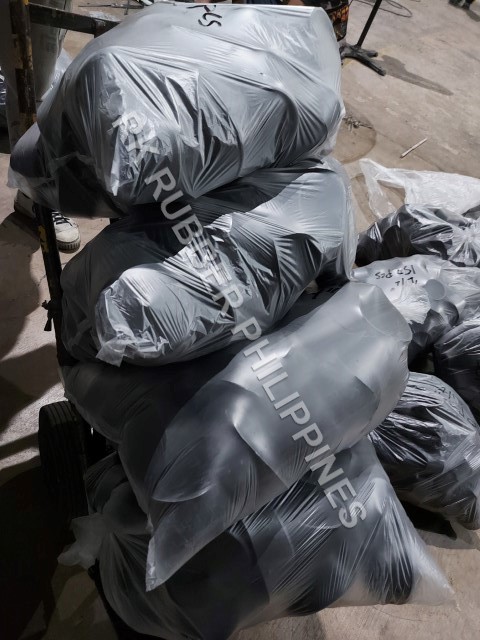
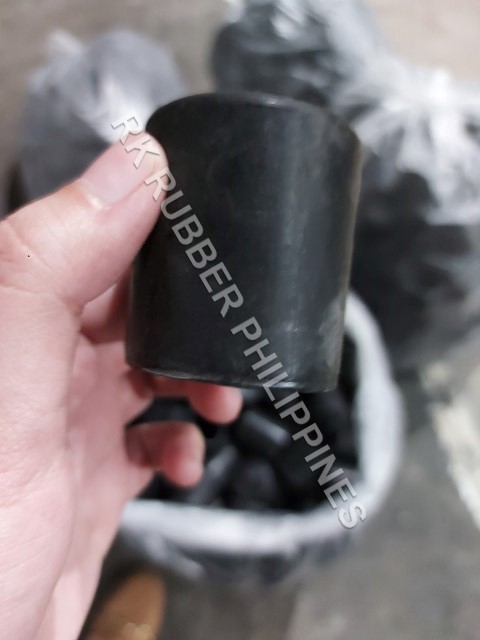